Digital Engineering Innovation
Seamlessly integrating the production site through the Digitalized Three Reality Philosophy
"Digital Engineering Innovation" is the basis of our two other concepts for manufacturing, "Autonomation Beyond Human Ability" and "Advanced Collaboration Between Human and Machines." Its objective is to implement the Digitalized Three Reality Philosophy by replicating on-site material objects to create an environment where their conditions can be accurately assessed from remote locations to deliver remote engineering that breaks down the barriers of time and place. This enables broad, objective, and quantitative visualization of on-site conditions, allowing you to analyze them for improvement and explore optimal operation measures, effectively accelerating the digital transformation of the manufacturing site and contributing to work process innovation.
Our Strengths
Offering as many as 200,000 control devices and control applications worldwide, all developed from an on-site perspective
Read more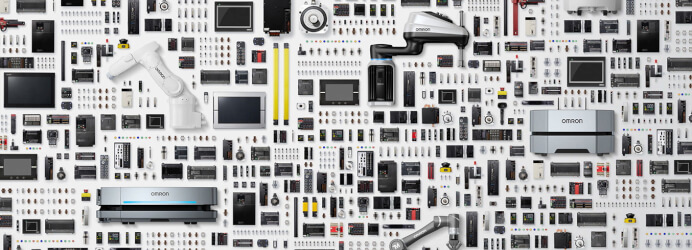