Top 4 challenges EV manufacturers face in their journey to achieving a sustainable future
Publicerat 17 juni 2024 i Sustainable Manufacturing
Electric vehicles (EVs) have transitioned from a niche market to a major industry force in recent years. As of 2023, electric cars account for nearly one in five vehicles sold, with sales increasing by 3.5 million units—a 35% jump from the previous year, according to the IEA's Global EV Outlook 2024. This surge is expected to continue, with projections indicating that sales in emerging markets will exceed 1 million units in 2024, marking a 40% increase from 2023. Governments worldwide are pushing to reduce CO2 emissions, which is speeding up this shift to electric vehicles.
So, what does this mean for automotive manufacturers? First, it means they need to pivot to designing and producing predominantly electric fleets, a move many have already started. Second, it means building new production lines and mastering new manufacturing processes, which can be quite a challenge.
This is where a trusted automation partner comes in. Partnering with an expert in automation can help manage the complexities of this industry-wide transition. With a broad technology portfolio, global support, and deep automotive expertise, OMRON is ready to guide manufacturers on their electrified journey.
This blog post will explore the top challenges in the EV manufacturing sector and how partnering with OMRON can provide effective solutions:
Challenge 1: Preventing overcharge, over-discharge, and overcurrent in battery packs
Solution: Battery and fuel cell manufacturing require precise control over the thickness of electrode sheets to prevent overcharge, over-discharge, and overcurrent. OMRON's solution involves double-sided thickness measurement, which gauges the thickness from both the upper and lower sides of the sheet, providing more accurate measurements than traditional single-sided methods.
Additionally, OMRON’s cell sorting solutions utilize RFID to manage time and cell capacity, and 2D codes to ensure that battery packs are produced from cells with identical capacities for consistent performance.
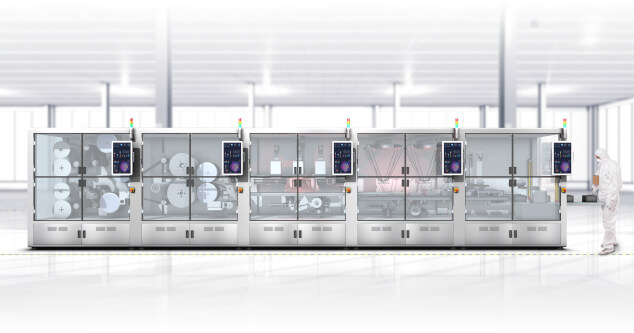
Challenge 2: Adapting to the increase of Electric Control Units (ECUs)
Solution: As vehicles become more electrified, the number of ECUs and their complexity increases. Traditional methods for configuring inspection settings for each connector pin are time-consuming.
OMRON's connector inspection solution simplifies this process by minimizing the need for complex algorithm design. This allows manufacturers to seamlessly integrate products into production, effectively managing associated costs while meeting the demands of a rapidly evolving industry.
Challenge 3: Enhancing the efficiency of welding inspection
Solution: The demand for rapid and accurate welding inspections is critical, especially in high-power motors with numerous weld points.
OMRON's advanced image processing technology enables non-stop and high-speed inspections, reducing the time traditionally required for quality checks. This technology uses a unique control algorithm for high-speed appearance inspection, significantly cutting down inspection times and maintaining high accuracy.
Challenge 4: Ensuring workforce safety in an automotive final assembly plant
Solution: In automotive final assembly plants, ensuring workforce safety is crucial. OMRON's autonomous mobile robots (AMRs), such as the LD Series and the heavy-duty HD-1500, are designed to reduce the need for forklifts, thereby enhancing safety and efficiency. These robots handle heavy payloads and navigate industrial environments autonomously, reducing the risk of injuries and addressing labor shortages effectively.
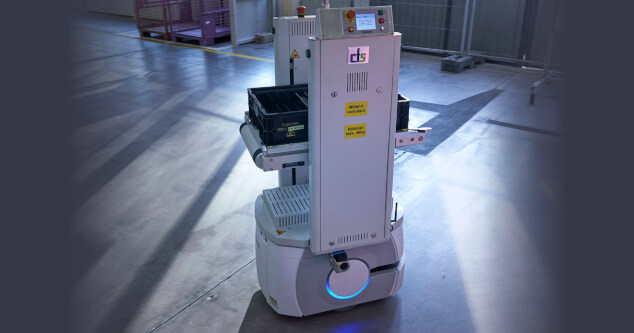